KAIZEN is a quality management method that originated in Japan's manufacturing industry. This term is now recognized in the business world globally. Let's take a closer look at the origins of KAIZEN, its fundamental principles, and its spread across the world.
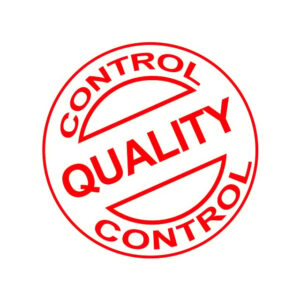
Origins of KAIZEN
KAIZEN was born in post-war Japan. Japanese companies cultivated a culture of making small, regular improvements to increase production efficiency. This continuous improvement effort became known as KAIZEN. The term KAIZEN means "continuous improvement" and refers to a business activity in which all employees are involved.

The Basics of KAIZEN
The concept of KAIZEN is simple. Rather than large-scale changes, it aims for significant overall results by accumulating small, daily improvements. This is most effective when all employees participate. KAIZEN is applied not only in manufacturing but also in various fields such as healthcare, psychotherapy, government, and banking.
Global Expansion
Since the 1980s, many foreign companies have come to learn from Japanese manufacturing. During this time, the KAIZEN methodology gained attention and was adopted by numerous countries and companies. It became particularly well-known for its success in the automotive and electronics industries, and KAIZEN emerged as a globally recognized quality management method. KAIZEN achieves overall productivity improvement by repeating small enhancements. This philosophy differs from the mid-20th century 'command and control' improvement programs.
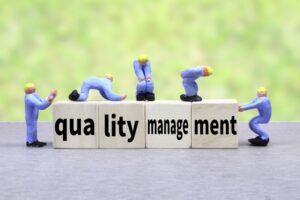
Implementing KAIZEN
KAIZEN is a Japanese-originated quality management method that focuses on continuous improvement in everyday processes. This approach seeks to enhance overall efficiency and productivity through small changes at all levels within an organization.
The Practice of KAIZEN
KAIZEN is a Japanese quality management method aimed at continuous improvement in daily processes. This method seeks to improve overall efficiency and productivity through small changes at every level within an organization.
The PDCA cycle (Plan → Do → Check → Action) is widely known as the core cycle in KAIZEN activities. This cycle functions as follows:
- Plan: Identify problems or opportunities and set goals. In this stage, strategies and action plans for improvement are developed.
- Do: Implement the planned improvements. Conduct small-scale tests or experiments to see how the plan works in the actual environment.
- Check: Evaluate the results of the implementation and analyze how effective they were in achieving the goals. Use the data and information obtained at this stage to move on to the next step.
- Action: Based on the insights gained in the Check stage, make necessary adjustments or changes. Then, transition to a new Plan stage and start the cycle again.
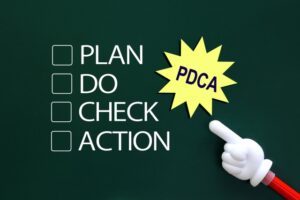
The practice of KAIZEN is deeply rooted in the culture and values of an entire organization. Every employee is encouraged to look at their work and processes and constantly ask, "Is there a better way?" By repeating such efforts, the organization as a whole can enhance its competitiveness and efficiency, achieving sustainable growth.
Although KAIZEN originated in the Japanese manufacturing sector, its simple and practical approach has been adopted by many companies around the world. This culture of continuous improvement will continue to support the success of many businesses in the future.